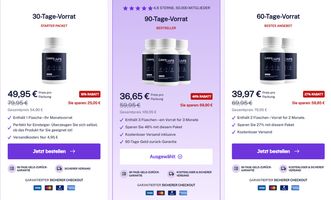
Lean Caps Deutschland
Lean Caps Deutschland: Die Revolution der Kappenproduktion durch Lean Management in Deutschland
In der heutigen, wettbewerbsintensiven Fertigungslandschaft sind Unternehmen zunehmend auf der Suche nach innovativen Methoden zur Optimierung ihrer Produktionsprozesse. Eine der erfolgreichsten Methoden ist das Lean Management, das darauf abzielt, Verschwendung zu minimieren und gleichzeitig die Qualität und Produktivität zu steigern. In Deutschland, einem Land, das weltweit für seine Ingenieurskunst und Effizienz bekannt ist, hat diese Methode zunehmend Einzug in viele Industrien gehalten.
Ein herausragendes Beispiel für den Erfolg von Lean Management in der deutschen Fertigung ist Lean Caps Deutschland. Das Unternehmen, das sich auf die Herstellung von Kunststoff- und Metallkappen für Branchen wie Getränke, Pharmazeutika und Konsumgüter spezialisiert hat, hat durch die Integration von Lean-Prinzipien in seine Produktionsprozesse nicht nur seine Effizienz erheblich verbessert, sondern auch einen neuen Standard in der Kappenfertigung gesetzt.
Was ist Lean Management?
Das Lean Management ist ein Managementansatz, der ursprünglich aus dem Toyota Produktionssystem (TPS) in Japan stammt und darauf abzielt, den Wert für den Kunden zu maximieren, indem Ressourcen, Zeit und Aufwand minimiert werden. Der Fokus liegt auf der Beseitigung von Verschwendung (auch als „Muda“ bekannt) in allen Formen. Verschwendung kann sich in folgenden Bereichen zeigen:
Überproduktion
Wartezeiten
Unnötiger Transport
Lagerbestände
Überflüssige Bewegung
Fehlerhafte Produkte
Nicht genutzte menschliche Ressourcen
Das Ziel des Lean Managements ist es, den Produktionsprozess effizienter zu gestalten, die Qualität zu erhöhen und die Produktionskosten zu senken, um wettbewerbsfähig zu bleiben.
Lean Caps Deutschland: Ein Beispiel für erfolgreiche Umsetzung von Lean-Prinzipien
Lean Caps Deutschland hat die Lean-Prinzipien übernommen, um die Produktion von Kappen und Verschlüssen für eine Vielzahl von Produkten wie Flaschengetränke und pharmazeutische Produkte zu optimieren. Angesichts von Herausforderungen wie steigenden Produktionskosten, langen Lieferzeiten und der Notwendigkeit, hohe Qualitätsstandards zu wahren, entschied sich das Unternehmen, Lean-Methoden in seine Fertigungsprozesse zu integrieren.
Die wichtigsten Maßnahmen, die Lean Caps Deutschland ergriffen hat, um Lean-Prinzipien umzusetzen, sind:
1. Wertstromanalyse und Prozessoptimierung
Der erste Schritt in der Transformation von Lean Caps Deutschland war die Durchführung einer Wertstromanalyse (Value Stream Mapping). Diese Methode hilft Unternehmen, den gesamten Produktionsprozess – von der Beschaffung der Rohmaterialien bis hin zum Versand des Endprodukts – visuell darzustellen und Verschwendung sowie Engpässe zu identifizieren.
Durch die Wertstromanalyse konnte Lean Caps Deutschland feststellen, dass bestimmte Fertigungsprozesse, wie beispielsweise die langen Umrüstzeiten zwischen verschiedenen Kappentypen, die Produktionsgeschwindigkeit verlangsamten. Durch die Neugestaltung von Arbeitsabläufen und die Beseitigung unnötiger Schritte konnte das Unternehmen die Produktionszeiten erheblich verkürzen und die Effizienz steigern.
2. Just-In-Time (JIT) Produktion
Ein zentraler Bestandteil des Lean Managements ist das Just-In-Time (JIT)-System, das darauf abzielt, Produkte nur dann zu produzieren und zu liefern, wenn sie benötigt werden – und zwar in der erforderlichen Menge und zur richtigen Zeit. Dieses Prinzip hilft dabei, Überbestände zu vermeiden und Lagerkosten zu reduzieren.
Lean Caps Deutschland hat eng mit seinen Lieferanten zusammengearbeitet, um die Lieferung von Rohmaterialien genau mit dem Produktionsplan abzustimmen. Durch die Einführung von JIT konnte das Unternehmen die Lagerbestände auf den Fertigungsböden erheblich reduzieren, was nicht nur Lagerkosten sparte, sondern auch die Produktionslinien flexibler und reaktionsschneller machte.
3. Kontinuierliche Verbesserung durch Kaizen
Ein weiteres zentrales Prinzip von Lean Caps Deutschland war die Einführung von Kaizen, was so viel wie „kontinuierliche Verbesserung“ bedeutet. Kaizen ermutigt alle Mitarbeiter, kontinuierlich nach Möglichkeiten zur Verbesserung der Arbeitsprozesse zu suchen, unabhängig davon, wie klein die Änderungen sein mögen.
Regelmäßige Kaizen-Workshops wurden eingeführt, bei denen Mitarbeiter aus verschiedenen Abteilungen zusammenarbeiteten, um Prozessprobleme zu identifizieren und Lösungen zu entwickeln. Diese Events förderten eine Kultur der Zusammenarbeit, bei der jeder Mitarbeiter Ideen zur Verbesserung des Produktionsprozesses einbringen konnte. So wurde beispielsweise der Wartungsplan für Maschinen verbessert und das Layout der Produktionshallen optimiert.
4. Standardisierte Arbeitsmethoden und 5S-System
Ein weiterer wichtiger Schritt war die Einführung von standardisierten Arbeitsmethoden und dem 5S-System. Standardisierte Arbeitsmethoden stellen sicher, dass jede Aufgabe auf die effizienteste Weise ausgeführt wird, indem bewährte Verfahren klar definiert werden. Dies trägt dazu bei, Variationen im Prozess zu minimieren und eine gleichbleibend hohe Qualität zu gewährleisten.
Das 5S-System konzentriert sich auf die Schaffung einer sauberen, organisierten und effizienten Arbeitsumgebung. Die fünf Schritte des 5S-Systems sind:
Sortieren: Unnötige Gegenstände aus dem Arbeitsplatz entfernen.
Ordnen: Werkzeuge und Materialien so anordnen, dass sie leicht zugänglich sind.
Sauberkeit: Den Arbeitsplatz regelmäßig reinigen und pflegen.
Standardisieren: Standardisierte Verfahren zur Aufrechterhaltung der Ordnung und Sauberkeit festlegen.
Sichern: Die oben genannten Praktiken kontinuierlich aufrechterhalten und weiterentwickeln.
Durch die Implementierung von 5S konnte Lean Caps Deutschland seine Produktionsflächen deutlich effizienter gestalten und gleichzeitig die Produktivität und Sicherheit am Arbeitsplatz erhöhen.
5. Mitarbeiterengagement und Schulung
Erfolgreiches Lean Management basiert nicht nur auf den richtigen Werkzeugen und Prozessen, sondern auch auf der aktiven Einbindung der Mitarbeiter. Lean Caps Deutschland setzte auf umfangreiche Schulungsprogramme, um alle Mitarbeiter in den Prinzipien des Lean Managements zu schulen und sicherzustellen, dass sie verstehen, wie ihre tägliche Arbeit zur Gesamtleistung des Unternehmens beiträgt.
Durch die Einbeziehung der Mitarbeiter in den kontinuierlichen Verbesserungsprozess konnte das Unternehmen nicht nur die Produktionsprozesse optimieren, sondern auch die Mitarbeiterzufriedenheit und das Engagement steigern.
6. Reduktion von Abfall und Steigerung der Nachhaltigkeit
Ein weiteres Ziel von Lean Caps Deutschland war die Reduzierung von Abfall und die Verbesserung der Nachhaltigkeit. Durch die Einführung von Lean-Prinzipien konnte das Unternehmen die Menge an Materialverschwendung in der Produktion erheblich verringern, was nicht nur die Produktionskosten senkte, sondern auch die Umweltbelastung reduzierte.
Zusätzlich setzte Lean Caps Deutschland auf eine energiesparende Produktion, optimierte den Wasserverbrauch und reduzierte Emissionen. Diese nachhaltigen Maßnahmen trugen dazu bei, die Umweltziele des Unternehmens zu erreichen und gleichzeitig die Kosten zu senken.
Ergebnisse der Lean-Implementierung
Die Implementierung von Lean-Prinzipien bei Lean Caps Deutschland führte zu einer Reihe von beeindruckenden Ergebnissen:
Erhöhte Effizienz: Durch die Beseitigung von Verschwendung und die Optimierung der Produktionsprozesse konnte das Unternehmen die Produktivität steigern und mehr Kappen in kürzerer Zeit produzieren.
Kürzere Durchlaufzeiten: Durch die Verbesserung des Materialflusses und der Lagerbestände konnte Lean Caps Deutschland die Produktionsdurchlaufzeiten erheblich reduzieren und so schneller auf Kundenanfragen reagieren.
Kostensenkungen: Die Reduzierung von Lagerbeständen, Ausschuss und Maschinenstillstandszeiten führte zu einer signifikanten Senkung der Produktionskosten.
Höhere Qualität: Durch die kontinuierliche Verbesserung der Prozesse und die strengen Qualitätskontrollen konnte das Unternehmen die Produktqualität steigern und die Fehlerquote verringern.
Verbesserte Mitarbeiterzufriedenheit: Die Einbeziehung der Mitarbeiter in den Verbesserungsprozess und die Förderung eines aktiven Austauschs führten zu höherer Motivation und geringerer Fluktuation.
Fazit
Lean Caps Deutschland ist ein ausgezeichnetes Beispiel dafür, wie Lean-Management-Prinzipien erfolgreich in der deutschen Fertigung angewendet werden können. Durch den Einsatz von Werkzeugen wie Wertstromanalyse, Just-In-Time-Produktion, Kaizen und dem 5S-System konnte das Unternehmen seine Prozesse optimieren, Kosten senken und die Qualität steigern.
Das Unternehmen zeigt, dass Lean Management nicht nur die Effizienz steigert, sondern auch zu einer nachhaltigeren und mitarbeiterfreundlicheren Produktion führt. In einer zunehmend globalisierten und wettbewerbsintensiven Welt stellt Lean Caps Deutschland unter Beweis, wie Unternehmen durch kontinuierliche Verbesserung und innovative Produktionsmethoden erfolgreich bleiben können.